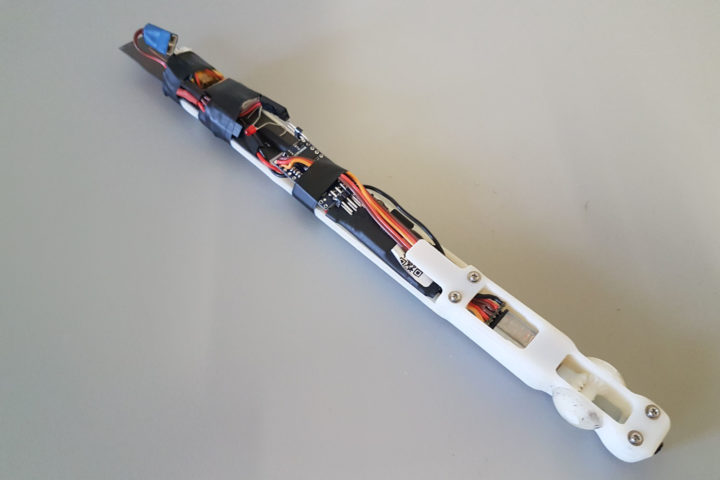
Wireless recharging pipe robot
Dr Bilal Kaddouh of the Self-Repairing Cities project has been working to develop a wireless recharging pipe robot designed to operate indefinitely within pipes, reducing the cost of inspection.
Wireless power transfer in metal pipes is a promising alternative to tethered exploration robots, with strong potential to enable longer operating times. Using the metal pipe as a wave guide drastically reduces the losses compared to free space and allows the use of higher transmit powers.
The prototype gas pipe inspection robot with wireless power receiver functionality was developed in collaboration with SWIFT project (EPSRC EP/N005686/1) that focuses on wireless power transfer technologies.
The pipe inspection robot is designed to fit a 1-inch pipe with sensors, microcontroller, wireless power transfer module and back-up batteries on-board. The design is fully 3D printed using
variable stiffness materials, and is fully operational straight out of the 3D printer. The current and previous revisions of the robot were printed in the EPSRC National Facility for Innovative
Robotic Systems at Leeds. The robot is equipped with a night vision camera, with the ability to extend longer to accommodate additional sensors. It has the potential to include infrared and
ultrasonic sensors depending on the inspection needs. The robot uses an encoder to measure distance travelled allowing preprogramed inspection routines and data logging.
Experiments on electromagnetic propagation in a metal pipe, as well as wireless power transfer for powering and charging of a prototype robot have been conducted[1]. The experiments successfully demonstrate Radio Frequency-to-Direct Current rectification with up to 23% efficiency at the end of a 2 metre long gas pipe, which can be used to extend the operating lifetime of an autonomous inspection robot. The best performance (23%, 18 mW direct current power, PDC) was obtained at a frequency of 12 GHz and 19 dBm of Radio Frequency power at the input of the rectifier.
The ability to transfer power wirelessly through the pipe allows the robot to operate for extended periods of time. This paves the way for future robots that remain in the pipeline system indefinitely while being charged wirelessly. Ultimately, this technology will reduce the cost of pipe inspection and allow detection of anomalies and cracks that facilitates preventive proactive maintenance.
The robot was also demonstrated at the Robotics Challenge event in June 2017 [video].
This case-study forms part of the project’s Mid-Term Report, which includes a full overview of the project, further case studies and sets out future work.
[1] Doychinov, V, Kaddouh, B, Mills, G et al. (3 more authors) (Accepted: 2017) Wireless Power Transfer for Gas Pipe Inspection Robots. In: To be confirmed. The UK-RAS Network Conference on Robotics and Autonomous System: robots working for and among us, 12 Dec 2017. (In Press)